by Biju Balakrishnan FIEAust CPEng NER
Principal Structural Engineer at Intrax PROJECTS
Water leaking and moisture ingress into buildings are the most reported failures in residential buildings. In a study conducted by Dr. Nicole Johnston (Deakin) in 2019, it was reported that the main contributor to building defects are water ingress/moisture.
The new wave of town houses and apartments which share common walls and floors between individual units creates another level of complexity. If water runs down to a neighbouring apartment or unit, whether it is due to bursting pipes or poor water proofing of the shower, the owner could be liable for creating nuisance to neighbours. This is in addition to unhealthy and dangerous conditions for the homeowner and loss of amenity. Water ingress can lead to durability issues and loss of structural integrity.
Unless designers, builders, and homeowners provide attention to design, installation, and maintenance, consequences can be huge repair costs and litigation. This article reviews some of the strategies in design and construction to avoid water leaking and moisture ingress in residential buildings, including multi units.
Introduction:
Is it a design, compliance, material, or installation issue?
In any building, residential or commercial, the building envelope protects occupants from all weather-related natural forces including water and moisture. In addition to this, water (hot and cold) is brought inside our building for our everyday consumption into our kitchens and bathrooms. Condensation is another source which, if not addressed, can lead to moisture and mould formation.
The main challenge is when water is dealt in a flat surface rather than in a pipe, for example, a flat roof, gutter, or shower base. Does the surface have the right slope? Is the material durable for water exposure? Can the joints perform well? Is water proofing designed and installed properly? There are many design challenges.
To have a good water/moisture proof building you need a good design, compliance to codes and standards, durable materials, correct installation, and maintenance.
Who is designing waterproofing and what standards are applicable?
Is it the architect, engineer, or builder? What standards are applicable?
Australian Institute of Waterproofing reports that the reason for failed waterproofing systems is mainly due to faulty installation (65%), inadequate design (30%) and wrong material choices (5%).
A proper waterproofed building requires a good design from architects and engineers. The general arrangement of various elements and choice of materials of a building plays a big part in achieving a watertight building. The reactive soils and unequal deflection of the buildings add another layer of complexity. The structural movements shall be limited to Appendix C of AS 2870.
There is very little a builder can do if the design is wrong. That doesn’t mean that the builder’s role is insignificant. Once the design is done, procuring right materials with warranty, and applying/installing to manufacturer’s specification is in the builder’s scope.
All building designers and practitioners shall ensure compliance to NCC 2019, Part 3.8.1 Wet areas and external waterproofing (Vol 2) and F1.7 Waterproofing of wet areas in buildings (Vol 1) in achieving a deemed-to-satisfy (DTS) solution.
External waterproofing shall be carried out to AS 4654.1:2012, AS 4654.2:2012 and AS 4858:2004. For internal wet areas, compliance to AS 3740:2021 is necessary. All substrates (concrete, masonry, plywood, cement sheet) shall conform to relevant Australian standards.
Where are the problem areas?
There are many areas where a faulty design or construction can lead to water/moisture ingress. Main building elements exposed to water and design requirements are described below.
1. Roof
In Australia, box gutters are designed to Annual Exceedance Probability (AEP) of 1% which is equivalent to Annual Recurrence Interval (ARI) of 100. A properly designed eaves and box gutter to AS/NZS 3500:2021-Part 3 Plumbing and Drainage will protect the building from an extreme event. This is more critical now with climate change, we are observing extreme events often, such as the recent floods in QLD and NSW.
Metal or tiled roofs generally perform well if the gutters are designed and maintained well. Internal box gutters are the main issue especially if they are not straight and don’t have an enough slope and overflow arrangements.
Many building elements require maintenance.
Even though the gutters are designed to last 50 years, the sealant will have a lifespan of less than 20 years. Therefore, all roof gutters require maintenance to ensure continuous performance.
Concrete roofs need a different treatment and generally exposed concrete is not a good choice for a roof due to the porous nature of concrete. Concrete and masonry are not “waterproofed” structures but are only “water resistant”. Water resistant structures will prevent moisture passage but will not hold water for long unless waterproofed.
Concrete roofs need waterproofing to keep water away. Since the waterproofing layer will be exposed to weather, the product selection is important, and needs to comply to AS 4654.1:2012. Ultraviolet protection and pedestrian traffic should also be considered in selecting external waterproofing membranes in a podium or balcony.
Having an extra metal roof over concrete is a common practice to avoid issues with concrete roofs. If this can be incorporated in the design, that is the best approach for concrete roofs.
2. Walls
Walls when integrated with openings (windows, openings) creates water ingress issue. Especially if window flashing and sealing is not carried out to standard practices. This is a common occurrence in new homes where the water ingress will be reported, mainly due to poor workmanship or material selection. All windows must comply to AS 2047:2014 and be tested to AS 4220.5 to ensure adequate weather protection.
Also cladding and cavity construction plays a bigger part in eliminating water from entering the building. Even though a cavity provides another barrier for moisture, a poorly ventilated and drained cavity can create condensation issues. Providing an approved sarking, flashing and weep holes are important to avoid condensation issues.
As bricks are a water absorbing material, brick walls require protection from the top (damp proof membrane and parapet flashing) and the bottom (damp proof membrane) to avoid moisture ingress and dampness.
3. Bathrooms and Showers
Showers and bathrooms are commonly prone to leakage in new buildings. Since there are different trades involved in installation, close supervision is required.
Having the right step down in the floor, water resistant substrate, proper waterproofing, screeding, tiling, and fixing of shower doors all must be done in the proper order. Builders generally engage an experienced sub-contractor to provide waterproofing to bathrooms and showers. Since the carpenters are providing the substrate and the wall, a close coordination between trades is required to achieve the best outcome. Water proofing compound is only a part of the total waterproofing systems and there are many factors involved in achieving a performing solution. One such example is the slope of waterproofed substrate (1 in 100).
Tile grouting shall be redone after 5 – 6 years and it is a part of maintenance which the owner is responsible for. Failed grouting can constantly wet the screed below and moisture can move horizontally to walls and rooms. This is a common occurrence in residential buildings after 5 years and house owners shall take special attention to any damaged grouts in showers and re grout if required.
4. Balconies
Balconies, even if protected by a roof, will get a fair amount of rain if exposed to open areas. Therefore, balconies shall be waterproofed to AS 4654.1/2:2012. The design and detailing of balconies play a bigger role in constructing a fool proof system. Having the right step down, enough slope in waterproofed substrate and finished floor finishes, proper membrane termination at external openings, doors and hobs are some of the many factors that need to be considered.
Selection of membrane will depend on whether the waterproofed surface is exposed or not exposed. Exposed membranes need to be checked as to whether the applied surface is trafficable or not. Performance of waterproofing membrane depends on dry film thickness, adhesion to substrate, and compatibility with adjacent surfaces, such as tile grout.
5. Foundation and Basements
Foundations are mostly concrete and must be designed to AS 2870:2011. Depending on the site reactivity, AS 2870 accommodates differential deflection up to 40mm. Due to these differential movements, cracking up to 0.3mm in rafts slabs is allowed. Since cracking is allowed, a concrete underlay (vapour barrier or damp proofing membrane) is a must under all foundations designed to AS 2870. Polyethylene film with a thickness of 0.2mm with adequate impact resistance shall be provided under all residential slabs.
Basements are prone to water ingress due to many reasons. Most of the ingress happens through retaining walls and the joint between basement slab and vertical wall. Selection of basement wall and construction method is based on soil conditions and how close the excavation is to site boundaries. If open cut excavation is possible, a fully tanked basement is practical whereas if the basement is pile and shotcrete, a wet basement is more appropriate to construct.
A fully tanked (or dry) basement is only required if habitable rooms are in the basement. If the basement is only used as a garage, a wet basement is a cost-effective solution. In a wet basement, the retaining wall is not waterproofed but water resistant. Water and moisture might penetrate the wall, but through proper design, the water and moisture can be managed by weep holes, linear drains, and discharge pits. Early communication is necessary with the client about the wet basement solution since if the expectation is for a dry basement, it can lead to conflicts and litigation. Also local council guidelines on discharging groundwater shall also be checked.
A fully tanked/waterproofed solution might be required if a habitable room is in the basement or when the water table is high. In such cases, basement waterproofing requires multiple strategies starting from behind the wall drainage, positive and negative waterproofing, water seals and concrete admixtures. Close coordination between structural engineers, drainage engineers, architects, and builders is necessary to come up with an appropriate basement wall design.
Conclusion
Building designers, engineers, certifiers and builders, all must work together to design a weather proofed building. Through adequate design and detailing, proper selection of waterproofing materials, quality installation and inspections, a performing solution can be implemented which will keep the building dry during its lifetime. Maintenance of the grouts/sealants are required which is the responsibility of the house owner.
Australia has unique weather, and many overseas certified products may not satisfy the performance requirement of NCC 2019. Therefore, compliance to AS 4654.1:2012 is required for all waterproofing materials. Compliance to AS 4654.2:2012 and AS 4654.2:2012 will ensure a good design and detailing.
Properly sized gutters, weather proofed windows, good cavity construction, damp proof membranes in brick walls, vapour barriers under footings slabs, basement waterproofing, there are many areas which need attention and competent design and installation.
Unless architects, engineers and builders work together a properly designed and installed waterproofing system is difficult to achieve. By engaging a competent design and construction team, a good installation quality control with adequate checks and a proper maintenance regime can create dry habitable buildings, and it is not rocket science.
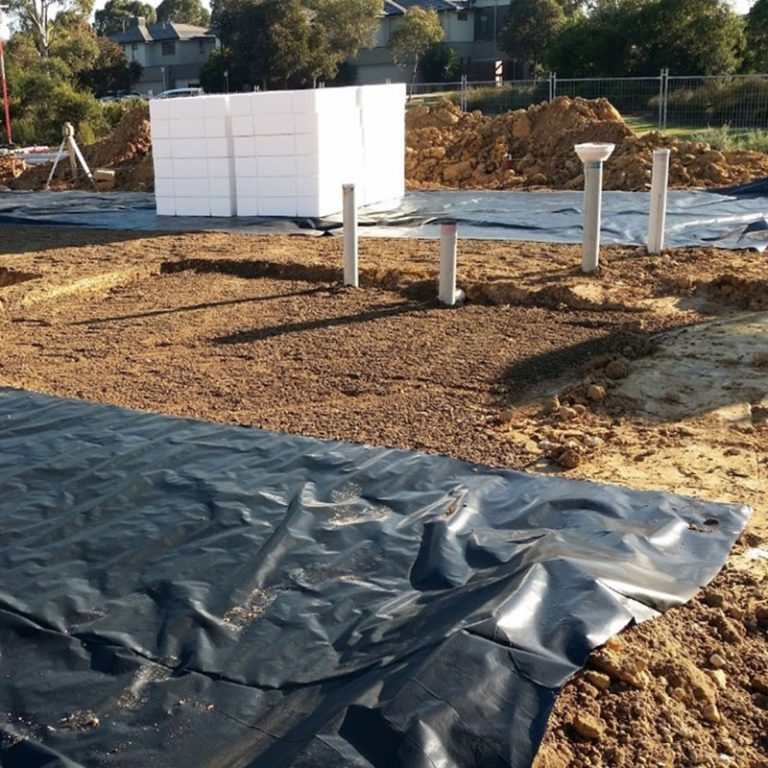
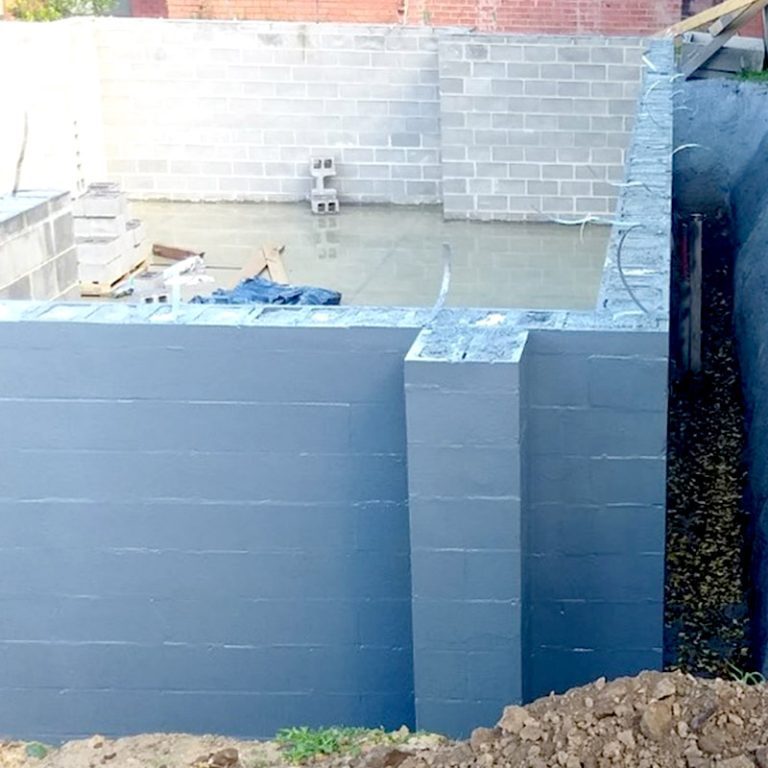
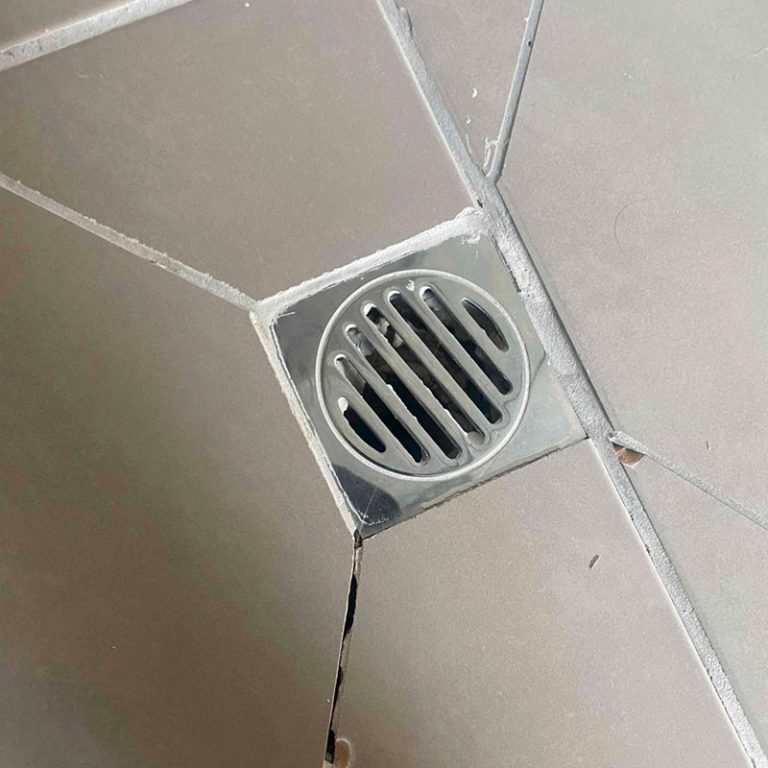
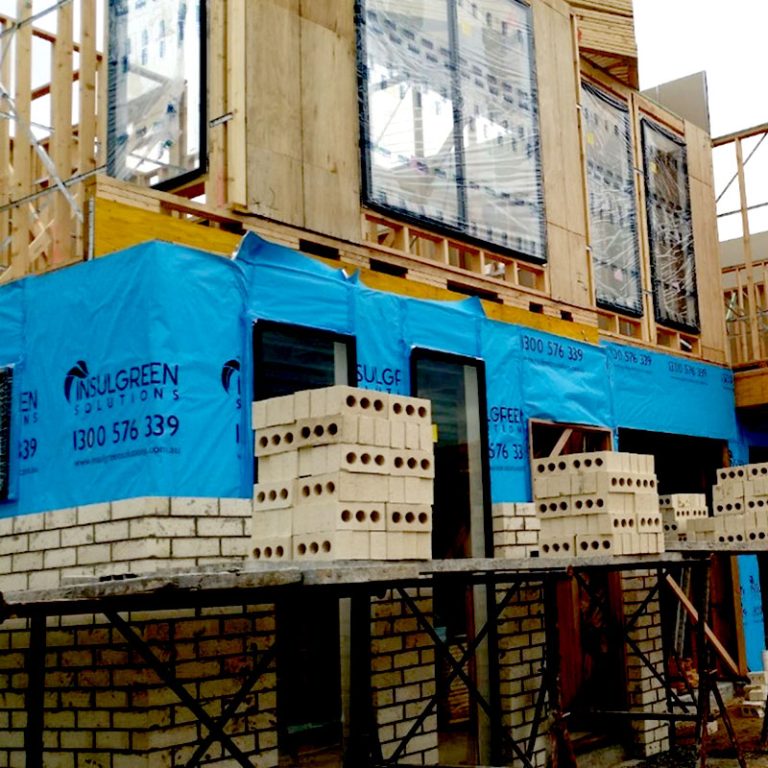